Packaging Line Is Vital For The Product Packaging Industry
A packaging line is a production line on which finished products are packaged to protect them during transport and handling before use. Packaging materials also provide a convenient surface to bear the imprints and codes that identify the product and allow regulators and buyers to track its progress through shipment to retailers or customers. In addition to packaging systems such as fillers, cartoners, case packers, and palletizers, most packaging lines include coding and marking equipment to apply basic codes that comply with regulations and enable accurate traceability. expeditions.
The efficiency of the packaging line will determine how quickly products move from stock to consumers. If you want to continue to generate profits and prevent inventory buildup, you need to have a solid understanding of how to measure your packaging line’s efficiency. Once you know how to identify inefficiencies on your packaging line, you can take the necessary steps to improve your overall packaging rate.
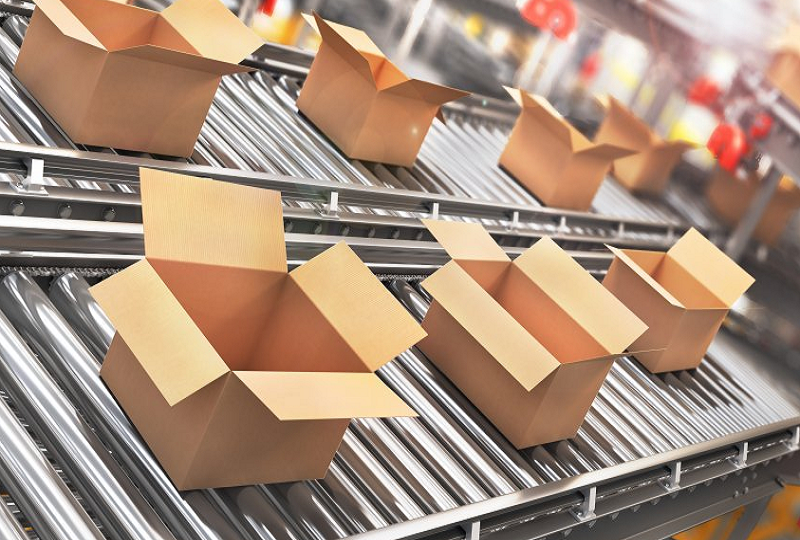
What is the Packaging Line?
Packaging lines use a wide range of packaging materials to wrap a wide variety of products, from soft to rigid, large to small, strong to flexible. To successfully mark these packaging materials, manufacturers have developed a variety of coding and marking machines, ranging from laser printers and engravers to continuous inkjet and thermal inkjet printers. This allows companies to choose the branding system that will most effectively utilize their unique packaging.
The packing line is where boxes are fed into the system, erected into their final shape, filled with the appropriate product, and before they are assembled onto pallets or sealed by other methods. This process can be done manually or using automated or semi-automated machines. Depending on the number of products you want to ship in a given period, you need to choose the right method to make your packaging line a success. Small batches may be labor intensive, while large batches may require automation for maximum packaging line efficiency.
How to Measure Packaging Line Efficiency?
To measure your packaging line efficiency, you’ll have to compare the actual output of materials to the expected output you create. When creating your expected output, you’ll need to be realistic based on the equipment and labor available to you. A small company without automation can’t expect to output as many products as a national company with fully-automated packaging lines.
You also need to factor in timing to your expected output. This means determining how many products should be sealed away each time your packaging line is run. The efficiency of your packaging line is timed only when it’s running. This means eliminating any time spent setting up or performing routine maintenance. These times will be factored into the total amount of time spent running the whole packaging system from setup to palletization, but they are not included in the time it takes your packaging line to complete a run.
Once you have your estimated output determined, you’ll want to monitor your packaging line to see if the actual output is similar or if there is a big difference in the numbers. If you find the actual output is not meeting your expectations, it’s time to think about how you want to improve the efficiency of your packaging line to reach the desired output of materials.
How to Recognize Areas of Improvement?
When monitoring the packaging line to determine its efficiency, you’ll want to make detailed notes about when the system stops, how long it’s stopped for, and why it stops in the first place. You’ll also want to recognize when production is slowed and why it’s slowed. There are a lot of factors that can determine when a system stops or slows, and identifying these situations is the first step to finding areas of improvement.
Often, stops in the system or slower periods of production are caused by the materials used. How packaging supplies are stored before use can affect how they perform on the production line. If materials are exposed to hazardous environments with high humidity or extreme temperatures, they won’t perform well during application. This remains true for fibrous boxes and cartons that can warp under pressure from their environment. When supplies are warped before use, they cannot be effectively run through machines for folding. This can cause machines to stop running or slow down to produce the erected box. Manual laborers also experience setbacks because warped materials are harder to form into the correct shape before filling.
Other improvements can be made by upgrading old and worn-down machines or switching to newer materials that are easier to work with. These changes are more expensive and time-consuming, but they should be done every few years when necessary to keep your packaging line up to speed with the latest improvements in the industry. You should be measuring your packaging line efficiency often to ensure your business goals are being met. When they are not being met, you should find ways to improve the system. If they are being met, then you know you have high packaging line efficiency. High efficiency allows you to maintain your profits by supplying the correct number of products in the right amount of time.
Now that you understand how to measure your packaging line efficiency and how to make improvements, you can optimize it to produce your desired output. There are endless ways to improve the packaging line, but you have to understand how to measure your current packaging line efficiency to get your starting point.
-
01
Further Discussion About Protein Bar Packing Machinery
27-02-2024 -
02
Sustain The Best Crispy With Automatic Packaging Machines
29-01-2024 -
03
Bread Packing Machine For Bakery Business
19-01-2024 -
04
How Flow Wrappers Are Adapting to Changing Trends
01-11-2023 -
05
The Comprehensive Guide to Packaging Machinery
31-10-2023 -
06
Automatic Cookie Packaging System Performance
01-09-2023 -
07
Streamlining Biscuit Packaging with Multipack Biscuit Packaging Machines
25-08-2023 -
08
From Assembly To Shipping: The Energy Bar Packaging Machine Does All
28-02-2023 -
09
Maximizing Efficiency With Food Packaging Machine Technology
22-02-2023 -
10
Clients Hunt For Professional And Functional Packaging Machine
10-11-2022